原材料信息从EBOM(Engineering Bill of Materials,工程物料清单)转换到ERP MBOM(Manufacturing Bill of Materials,生产物料清单)的过程涉及将设计阶段的产品组件信息转化为生产阶段需求的材料信息。这一过程是至关重要的,它确保了设计理念能够无缝地转化为实际生产工序。核心转换步骤包括:物料识别和分类、序列化和版本控制、制造过程分解、物料需求量计算等。在转换中,物料识别和分类尤为关键,因为它涉及到将各个零件和原材料依据其特性和用途分类,确保生产过程中材料的正确性和充分性。
一、物料识别和分类
在将EBOM转换为MBOM的过程中,物料识别和分类是第一步,旨在确保正确识别EBOM中的每个组件,并根据它们在生产过程中的用途和需求进行合适的分组。分类的准确性关系到后续步骤中成本计算、采购计划和生产调度的效率。
- 分类过程中需要对照设计图纸,将所有原材料和半成品按其属性(如材质、尺寸等)进行划分。
- 同时应考虑到生产过程中的特殊要求,比如温度耐受、强度等级或是兼容性问题,以确定是否需要为某一特定环节引入特殊材料或改进现有材料。
二、序列化和版本控制
任何产品在制造过程中都可能经历设计变更,这就要求在物料清单转换过程中要有序列化和版本控制。这样可以保证每次生产都使用最新的、已经审批的设计文档和物料清单。
- 序列化是赋予每个部件一个独特的序列号,便于跟踪和质量控制。
- 版本控制则确保了所有部门在任何给定时刻都使用正确的设计数据,减少了错误和返工的可能性。
三、制造过程分解
在MBOM中,原材料和组件信息需要与具体的制造工序相关联。这通常涉及将整个制造过程细分为若干步骤,并明确各步骤所需的原材料和部件。
- 制造过程分解需要专业的生产知识,以确保每一步骤都可执行,且资源分配合理。
- 在这个阶段,工艺工程师会参与其中,以确保MBOM反映出最有效的生产方式。
四、物料需求量计算
准确的物料需求量计算是确保生产效率和降低成本的关键。在EBOM转为MBOM时,需要将设计阶段的原材料信息转换成具体生产过程中的实际用量。
- 物料需求量的计算应考虑到生产过程的损耗、废料和预期的产品合格率。
- 优化物料使用量,不仅能减少浪费,还能降低库存成本。
相关问答FAQs:
1. 如何将EBOM中的原材料信息转换到ERP MBOM中?
在将EBOM中的原材料信息转换到ERP MBOM中时,首先需要进行数据清洗和整理。这包括对EBOM中的原材料清单进行检查,确保每个原材料的命名一致,并且去除重复的条目。接下来,根据MBOM的要求和结构,进行原材料信息的映射和转换。这包括确定每个原材料的编号、规格、描述以及单位等信息,并将其与MBOM中的相应原材料进行匹配。
2. 如何确保EBOM中的原材料信息准确转换到ERP MBOM中?
为确保EBOM中的原材料信息准确转换到ERP MBOM中,一种有效的方法是进行验证和审查。在转换过程中,可以设置审查人员对原材料信息进行核对,确保其准确性和一致性。同时,可以利用软件工具或自定义脚本来自动化部分转换过程,进一步提高数据准确性。在转换完成后,还应进行最终的验证,包括与实际生产中使用的原材料进行对比,以确保转换后的信息与实际情况一致。
3. 在EBOM转换为ERP MBOM过程中可能遇到哪些挑战?如何应对?
在将EBOM转换为ERP MBOM的过程中,可能会遇到一些挑战。其中一个挑战是数据格式和结构的差异。EBOM和ERP系统之间可能存在不同的命名约定和数据格式,这可能导致信息转换困难。为应对这种挑战,可以通过使用数据转换工具或编写自定义脚本来实现数据的格式和结构转换。
另一个挑战是原材料编号和规格的匹配。EBOM中的原材料可能使用不同的编号方式和命名约定,与MBOM中的原材料命名不一致。为解决这个问题,可以进行手动匹配和映射,或者使用基于模糊匹配算法的自动化工具来帮助提高匹配的准确性。
此外,还可能遇到原材料信息缺失或不完整的情况。在转换过程中,可能会发现一些原材料的信息不完整,需要与相关部门或供应商进行沟通和确认。在处理这种情况时,及时与相关人员进行沟通并补充完整信息,以确保转换后的MBOM中的原材料信息准确无误。
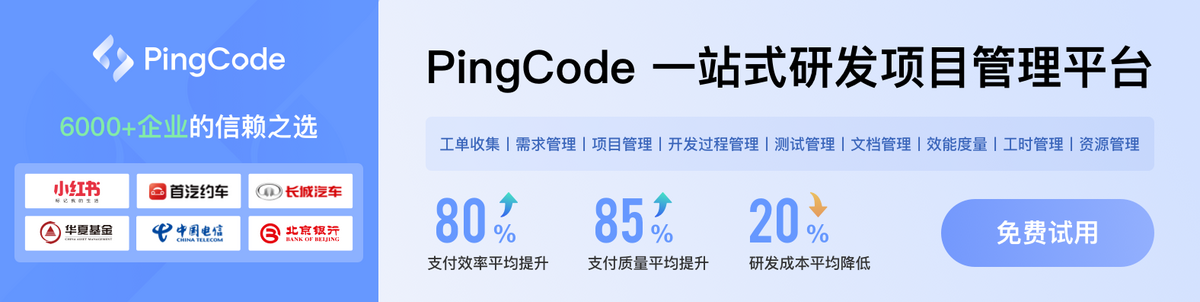