KPIs, or Key Performance Indicators, are vital metrics used to monitor and improve production processes by providing clear targets and measurable outcomes、benchmarking agAInst industry standards、identifying inefficiencies、driving employee performance、 and enabling informed decision-making. 通过提供明确的目标和可衡量的结果,KPIs allow managers to gain insight into the effectiveness of their production strategies, make data-driven adjustments, and ultimately enhance productivity and quality.
通过提供明确的目标和可衡量的结果,KPIs allow for continuous monitoring and adjustment of the production line. Specific KPIs such as cycle times, yield rates, and equipment efficiency can pinpoint where bottlenecks or waste are occurring. By analyzing these metrics, managers can introduce targeted improvements, optimize resource allocation, and streamline workflows to enhance overall production performance.
一、DEFINING RELEVANT KPIS
Understanding which KPIs to monitor is essential for any production process. Depending on the industry and specific company goals, relevant KPIs could include Productivity Rates, Quality Control Metrics, Cycle Time, and Maintenance Downtime.
When defining Productivity Rates, it is not only about the quantity produced but also about the effective utilization of resources. A high productivity rate indicates a streamlined process with minimal waste. Examining the individual performance of departments and machines helps identify areas for improvement.
Quality Control Metrics are crucial for maintaining high standards. KPIs such as defect rates or the percentage of products meeting quality criteria ensure that the production process yields items that satisfy customer expectations and minimize returns or recalls.
二、TRACKING AND ANALYZING KPIS
Regular tracking and analysis of KPIs enable continuous monitoring and improvement of the production process. Utilizing data analysis tools and software can help in managing these indicators effectively.
One critical aspect of tracking KPIs is Real-Time Monitoring. This approach allows for immediate corrective actions if a process deviates from the set parameters. For instance, if the cycle time increases unexpectedly, managers can instantly investigate and resolve the issue, minimizing downtime.
Analyzing trends over time is also vital. KPI historical data can help to identify patterns that may indicate underlying problems. By conducting a Root Cause Analysis when a KPI benchmarks are not met, companies can develop strategic solutions that prevent recurrence of the same issues.
三、BENCHMARKING KPIs
Benchmarking involves comparing a company’s KPIs with industry standards or best practices to gauge performance and identify areas that need attention. Competitive Benchmarking and Strategic Benchmarking are two approaches commonly used.
Competitive Benchmarking involves comparing your KPIs with those of direct competitors to determine where you stand in the market. This can highlight competitive weaknesses and strengths, guiding where to allocate resources to improve performance.
With Strategic Benchmarking, companies look beyond their immediate competitors and compare their KPIs with organizations known for their outstanding production processes. This broader perspective can inspire innovative improvements and strategic shifts that lead to superior performance.
四、USING KPIS TO DRIVE PERFORMANCE
KPIs play a crucial role in motivating and guiding employees towards achieving production goals. Setting clear KPI-based objectives and providing regular feedback can significantly enhance performance.
By utilizing Performance Dashboards, employees at all levels get a visual representation of how their actions impact overall production KPIs. This can foster a culture of accountability and continuous improvement.
Incentive Programs tied to KPI achievements are another way to motivate staff. When employees understand that their efforts contribute to measurable outcomes, they are more likely to take initiative and work toward enhancing those metrics.
五、MAKING INFORMED DECISIONS WITH KPIS
KPIs provide the quantitative foundation for making informed decisions about the production process. They enable scenario planning, investment decisions, and strategic choices that are grounded in empirical data.
Scenario Planning with KPIs helps managers to predict outcomes based on different variables, such as changes in demand, new equipment installations, or shifts in supplier dynamics. This predictive capacity is essential for making preemptive adjustments and strategic planning.
When considering Investment Decisions, KPIs can indicate which areas of the production line would benefit the most from capital infusion. For example, if the efficiency KPIs for a particular machine are consistently low, it may be time to consider upgrading or replacing it.
六、OPTIMIZING PROCESSES USING KPIS
KPIs provide valuable insights that help optimize manufacturing processes. They identify the stages where automation can boost efficiency, where quality can be improved, and where costs can be cut without compromising outputs.
Automation Opportunities can be identified by analyzing KPIs that point to repetitive tasks or bottlenecks. Implementing automation in these areas can drastically increase production speeds and reduce human error.
Quality improvement is often a focus of production process optimization. KPIs related to product quality can highlight specific points in the process that need refinement, helping to reduce defect rates and improve customer satisfaction.
七、MANAGING RISKS WITH KPIS
KPIs can also indicate risks in the production process and help in developing strategies to mitigate them. Predictive maintenance, for example, can be planned based on KPIs related to equipment performance and failure rates.
Predictive Maintenance KPIs such as Mean Time Between Failures (MTBF) and Mean Time To Repair (MTTR) guide the scheduling of maintenance tasks. This approach avoids unexpected downtime and extends the lifespan of machinery.
Monitoring KPIs related to SAFety incidents allows management to address potential hazards proactively. This not only protects employees but also ensures that production processes are not interrupted due to avoidable accidents.
KPIs are instrumental in enhancing production processes by delivering actionable insights and driving efficiency across operations. By continuously tracking, analyzing, and optimizing these indicators, businesses can sustain a competitive edge and achieve their production objectives.
相关问答FAQs:
问题1:KPI是如何在生产流程中发挥作用的?
答:KPI(关键绩效指标)是用于衡量和监控公司或部门的业绩的关键指标。在生产流程中,KPI可以帮助公司确定和衡量关键的生产绩效指标,如产量、质量水平、生产效率等。通过设定和追踪这些指标,公司能够及时监控生产流程中的问题和瓶颈,并及时采取措施加以改进。例如,如果生产效率KPI低于预期,可以通过优化工艺流程、提高设备效能等方式来改进生产效率。
问题2:KPI如何帮助实时监控生产流程?
答:通过设定和追踪合适的KPI指标,可以实时监控生产流程的关键指标,并对偏离预期的情况做出及时反应。例如,设定每小时产量KPI,可以实时监控生产线的产量是否符合预期,一旦产量低于预期,就能够及时发现并采取措施解决问题。另外,KPI也可以与生产线数据采集系统结合,实时将数据反馈给监控系统,通过可视化的界面直观地显示生产流程的状态。
问题3:KPI如何帮助改进生产流程的质量?
答:KPI可以帮助公司确定和追踪关于品质的指标,如产品不合格率、返工率等,通过设定合适的目标值和持续追踪,公司可以及时发现质量问题并采取措施改进。例如,如果不合格率超过设定的目标值,可以进行质量问题的根本原因分析,通过改进工艺、提高员工培训等方式来提升产品质量。同时,KPI指标的设定也可以激励员工在质量控制方面发挥更大的积极性和责任心。
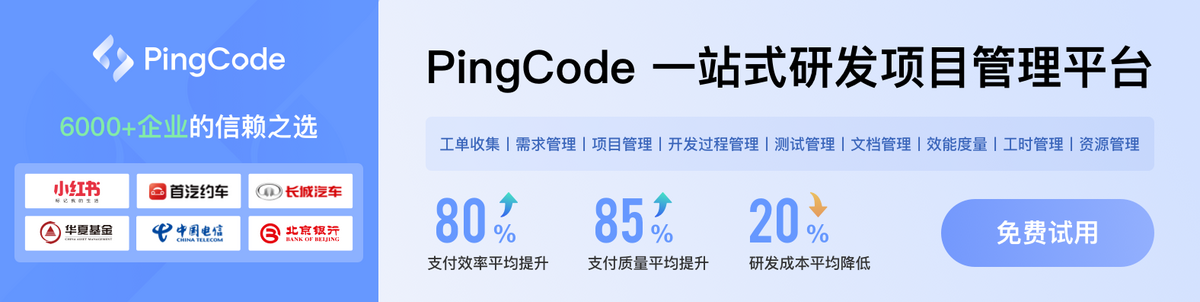