PLC(可编程逻辑控制器)是一种用于自动化控制的电子设备,广泛应用于工业生产中的自动化控制与监控。基于PLC的配料生产线控制系统的设计,需要集成传感器信号采集、配比控制算法、人机交互界面、网络通信等要素。这样的系统设计应确保生产过程的稳定性、准确性和灵活性,以满足现代化生产的要求。系统设计的核心在于开发高效、可靠的PLC程序,并与相关的硬件设备如电机、传感器、变频器等无缝集成。
其中,配比控制算法是系统设计的核心之一,确保各种原料按照精确比例混合。这通常涉及对流量、重量等参数的准确检测,并根据实际配料要求动态调整输出,以保持配比的一致性。
一、系统总体设计概述
设计基于PLC的配料生产线控制系统时,首先需要确定整个系统的框架和组成部分。系统通常包含输入/输出(I/O)单元、控制处理单元、操作界面(HMI)、通信接口和驱动执行单元。
I/O单元
I/O单元主要负责与现场传感器及执行机构间的信号交换。输入部分接收诸如重量、温度等传感器信号,输出部分则驱动各种执行机构,比如开关阀门和启动电机。
控制处理单元
控制处理单元是系统的大脑,其中运行PLC程序,执行各类控制算法和逻辑判断。这部分需要对各输入信号进行实时处理,并输出相应的控制信号。
二、传感器信号采集与处理
传感器信号采集是自动化配料系统设计的基础。精确的信号采集保障了系统按照预定配方进行精确配料。
选择传感器
根据需要监控的参数,选择相应的传感器。例如,使用称重传感器来监控物料的重量,使用流量计测量液体原料的流入量。
信号处理
采集到的模拟信号通常需要通过模拟/数字转换器(A/D转换器)转换为数字信号,PLC才能进行处理。信号可能需要过滤、放大和校准等处理以确保准确性。
三、配比控制算法实现
配料配比的准确执行是配料生产线的核心任务,配比控制算法的优劣直接关系到最终产品的质量。
设置配方
通过配料生产线控制系统设置配方参数,包括各种原料的比例与顺序。
实现PID控制
PID(比例-积分-微分)控制算法是实现精准配料控制的常用方法,PLC需要实时调整输出以减少配料误差。
四、人机交互界面设计
操作界面或者HMI(Human Machine Interface)是操作人员与控制系统之间的桥梁。高效直观的操作界面能大幅提升操作效率和系统的易用性。
界面布局
设计简洁直观的界面布局,确保操作人员能够快速理解系统状态并进行操作。
功能实现
包括实时显示系统参数、记录生产数据、配方输入与修改、故障诊断及报警系统等。
五、网络通信与数据集成
在现代工业环境中,PLC往往需要与其他系统如企业资源规划(ERP)系统、制造执行系统(MES)等进行通信。
网络协议
选择合适的工业通信协议如Modbus、Profibus或EtherNet/IP来实现各系统之间的数据交换。
数据集成
确保数据的顺畅流动和集成,以便进行生产监控、数据分析和远程维护等。
通过上述详细的设计步骤,可以建立一个基于PLC的配料生产线控制系统,该系统能够通过自动化控制、精确配比和高效的人机交互来满足现代工业生产线的需求,确保配料过程的高效性、稳定性和可追踪性。
相关问答FAQs:
1. 配料生产线控制系统的设计需要考虑哪些因素?
在设计基于PLC的配料生产线控制系统时,需要考虑以下因素:
- 生产线的规模和复杂性:根据生产线的规模和复杂性,确定所需的PLC数量和类型,并选择适当的网络通信协议。
- 数据采集和监测要求:确定需要监测和采集的数据类型和参数,例如温度、压力、流量等,并选择合适的传感器和仪表。
- 控制逻辑和算法:根据生产线的工艺过程和产品要求,设计控制逻辑和算法,确保系统能够实现精确的配料和控制操作。
- 系统的可靠性和安全性:考虑系统的可靠性和安全性要求,选择合适的备份和恢复策略,并确保系统能够及时检测和响应故障事件。
- 人机界面和操作方式:设计直观易用的人机界面,方便操作员对系统进行监控和调整,提供必要的报警和提示信息。
2. 如何选择合适的PLC和其他硬件设备?
在选择合适的PLC和其他硬件设备时,需要考虑以下几个因素:
- 适用场景和要求:根据配料生产线的规模、复杂性和控制要求,确定所需的PLC类型和性能参数,例如输入/输出点数、运算速度、通信接口等。
- 可靠性和稳定性:选择具有较高可靠性和稳定性的PLC品牌和型号,减少故障和停机时间。
- 扩展性和兼容性:考虑系统的扩展性和兼容性要求,选择支持多种通信协议和接口的PLC,以便与其他设备和系统进行连接与集成。
- 成本效益:综合考虑PLC和其他硬件设备的价格、质量和功能,选择性价比最高的产品。
3. 如何提高配料生产线控制系统的效率和精度?
要提高配料生产线控制系统的效率和精度,可以采取以下措施:
- 优化控制算法:不断优化控制算法,根据实际情况进行调整和改进,确保控制操作的准确性和稳定性。
- 使用高精度传感器和仪表:选择高精度的传感器和仪表,提供准确的数据反馈,以确保配料和控制操作的精度。
- 自动化控制和协同作业:引入自动化控制和协同作业技术,减少人为干预和误操作,提高系统的响应速度和稳定性。
- 数据分析和优化:使用数据分析工具对生产过程进行监测和优化,识别潜在问题并及时采取措施,提高生产效率和产品质量。
- 定期维护和保养:定期进行设备维护和保养,保持设备的正常运行状态,避免故障和停机造成的生产损失。
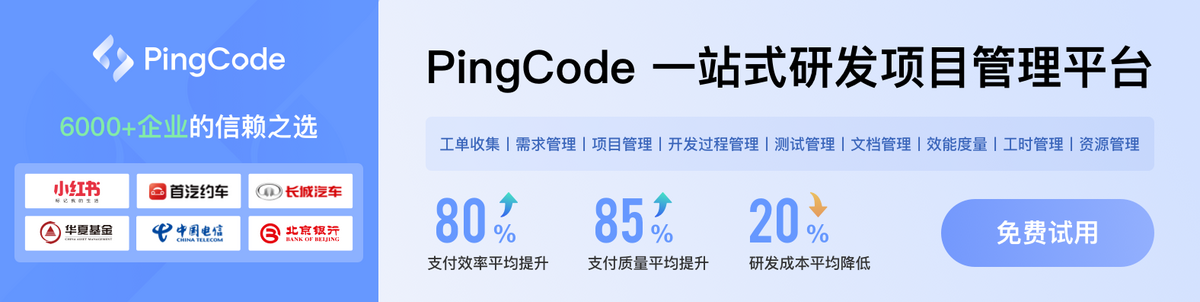