化工厂常用的控制系统包括DCS(分布式控制系统)、PLC(可编程逻辑控制器)、SCADA(数据采集与监视控制系统)、MES(制造执行系统)。其中,DCS和PLC是化工厂中最为常见的控制系统。DCS主要用于过程控制,适用于复杂的多变量控制和大规模生产场景。PLC则主要用于逻辑控制和离散制造的场景,适应性强且易于维护。接下来,我们将详细讨论这些控制系统的特点、应用场景及其在化工厂中的实际应用。
一、DCS(分布式控制系统)
DCS的特点
DCS,分布式控制系统,是一种多层次的自动化系统,广泛应用于过程控制领域。其特点包括:
- 分布式架构:DCS系统的控制器、操作站和工程站等各个部件分布在整个工厂中,每个单元都有独立的处理能力。
- 强大的数据处理能力:DCS能够同时处理大量的实时数据,适用于复杂的化工过程。
- 高可靠性和可用性:由于其冗余设计,DCS系统具有很高的可靠性,能够保证系统的连续运行。
- 灵活的配置和可扩展性:DCS系统可以根据具体需求进行配置,并且易于扩展和升级。
DCS的应用场景
DCS系统适用于大型化工装置和复杂的过程控制场景,包括但不限于以下:
- 炼油厂:涉及多个复杂的化学反应和物理过程,需要实时监控和调节。
- 化肥厂:原材料的处理和合成过程复杂,需要精确控制。
- 制药厂:生产过程中对温度、压力等参数要求严格,需实时监控和调整。
- 石化企业:复杂的生产流程和高风险的操作环境,需要高可靠性的控制系统。
DCS在化工厂的实际应用
在化工厂中,DCS系统通常用于实时监控和控制生产过程。以下是DCS系统在化工厂中的一些实际应用:
- 过程控制:DCS系统能够实时监控化工过程中的各种参数(如温度、压力、流量等),并根据预设的控制策略进行自动调节,以确保生产过程的稳定和高效。
- 报警管理:DCS系统能够实时检测生产过程中出现的异常情况,并及时发出报警信号,帮助操作人员快速排除故障。
- 数据记录与分析:DCS系统能够实时记录生产过程中的各种数据,并通过数据分析工具对数据进行处理,以优化生产过程和提高生产效率。
- 远程监控与维护:DCS系统支持远程监控和维护,操作人员可以通过网络远程访问系统,进行实时监控和故障排除。
二、PLC(可编程逻辑控制器)
PLC的特点
PLC(可编程逻辑控制器)是一种用于工业自动化控制的数字计算机,其特点包括:
- 高可靠性:PLC具有较高的抗干扰能力和稳定性,适用于工业现场恶劣的环境条件。
- 灵活性和可编程性:PLC可以根据实际需求进行编程,灵活实现各种控制功能。
- 易于维护:PLC的模块化设计使其易于维护和更换,降低了维修成本。
- 实时性:PLC具有很高的实时性,能够快速响应生产过程中的各种变化。
PLC的应用场景
PLC系统适用于各种工业自动化控制场景,包括化工厂的以下应用:
- 设备控制:如搅拌机、泵、阀门等设备的控制。
- 生产线自动化:如输送带、包装机等生产线设备的自动化控制。
- 安全监控系统:如火灾报警系统、气体泄漏检测系统等。
- 过程控制:如温度、压力、流量等参数的实时监控和调节。
PLC在化工厂的实际应用
在化工厂中,PLC系统通常用于实现设备的自动化控制和过程控制。以下是PLC系统在化工厂中的一些实际应用:
- 设备自动化控制:PLC系统能够实现化工设备的自动化控制,如搅拌机、泵、阀门等设备的启停控制和状态监测。
- 生产线自动化:PLC系统能够实现生产线设备的自动化控制,如输送带、包装机等设备的自动运行和状态监控。
- 安全监控系统:PLC系统能够实时监控生产过程中的安全参数,如火灾报警系统、气体泄漏检测系统等,并在出现异常情况时及时发出报警信号。
- 过程控制:PLC系统能够实时监控和调节生产过程中的各种参数,如温度、压力、流量等,以确保生产过程的稳定和高效。
三、SCADA(数据采集与监视控制系统)
SCADA的特点
SCADA(数据采集与监视控制系统)是一种用于远程监控和控制工业过程的系统,其特点包括:
- 远程监控与控制:SCADA系统能够实现对远程设备和过程的实时监控和控制。
- 数据采集与分析:SCADA系统能够实时采集生产过程中的各种数据,并通过数据分析工具对数据进行处理和分析。
- 报警管理:SCADA系统能够实时检测生产过程中的异常情况,并及时发出报警信号。
- 可视化界面:SCADA系统通常具有直观的可视化界面,操作人员可以通过界面实时监控和控制生产过程。
SCADA的应用场景
SCADA系统适用于需要远程监控和控制的工业自动化场景,包括化工厂的以下应用:
- 远程设备监控:如远程泵站、输油管道等设备的实时监控和控制。
- 过程监控:如化工生产过程中的温度、压力、流量等参数的实时监控和调节。
- 数据采集与分析:如生产过程中的数据采集、存储和分析。
- 报警管理:如生产过程中的异常情况检测和报警管理。
SCADA在化工厂的实际应用
在化工厂中,SCADA系统通常用于实现远程监控和控制生产过程。以下是SCADA系统在化工厂中的一些实际应用:
- 远程设备监控:SCADA系统能够实现对远程设备的实时监控和控制,如远程泵站、输油管道等设备的状态监测和控制。
- 过程监控:SCADA系统能够实时监控和调节生产过程中的各种参数,如温度、压力、流量等,以确保生产过程的稳定和高效。
- 数据采集与分析:SCADA系统能够实时采集生产过程中的各种数据,并通过数据分析工具对数据进行处理和分析,以优化生产过程和提高生产效率。
- 报警管理:SCADA系统能够实时检测生产过程中出现的异常情况,并及时发出报警信号,帮助操作人员快速排除故障。
四、MES(制造执行系统)
MES的特点
MES(制造执行系统)是一种用于管理和优化生产过程的系统,其特点包括:
- 生产计划管理:MES系统能够根据生产计划合理调度资源,优化生产过程。
- 生产过程监控:MES系统能够实时监控生产过程中的各种参数,确保生产过程的稳定和高效。
- 质量管理:MES系统能够实时监控生产过程中的质量参数,确保产品质量。
- 数据分析与决策支持:MES系统能够通过数据分析工具对生产过程中的数据进行处理和分析,提供决策支持。
MES的应用场景
MES系统适用于需要精细化管理和优化生产过程的工业自动化场景,包括化工厂的以下应用:
- 生产计划管理:如生产计划的制定、资源调度等。
- 生产过程监控:如生产过程中的温度、压力、流量等参数的实时监控和调节。
- 质量管理:如生产过程中的质量参数监控和管理。
- 数据分析与决策支持:如生产过程中的数据采集、存储和分析,提供决策支持。
MES在化工厂的实际应用
在化工厂中,MES系统通常用于管理和优化生产过程。以下是MES系统在化工厂中的一些实际应用:
- 生产计划管理:MES系统能够根据生产计划合理调度资源,优化生产过程。如根据生产计划安排设备的运行和维护,确保生产过程的连续和高效。
- 生产过程监控:MES系统能够实时监控生产过程中的各种参数,如温度、压力、流量等,确保生产过程的稳定和高效。如实时监控反应釜的温度和压力,及时调节加热和冷却系统,以保持反应的稳定。
- 质量管理:MES系统能够实时监控生产过程中的质量参数,确保产品质量。如实时监控产品的成分、纯度等质量参数,及时调整生产工艺,确保产品质量符合要求。
- 数据分析与决策支持:MES系统能够通过数据分析工具对生产过程中的数据进行处理和分析,提供决策支持。如通过分析生产过程中的数据,发现生产过程中的瓶颈和问题,提出改进措施,提高生产效率和产品质量。
五、综合应用
在实际应用中,化工厂通常会综合使用DCS、PLC、SCADA和MES系统,以实现生产过程的自动化和优化管理。以下是一些综合应用的案例:
- 综合自动化控制:在化工厂中,DCS系统通常用于实现过程控制和数据采集,PLC系统用于设备的自动化控制,SCADA系统用于远程监控和报警管理,MES系统用于生产计划管理和数据分析。通过综合应用这些系统,化工厂能够实现生产过程的自动化和优化管理,提高生产效率和产品质量。
- 生产过程优化:通过综合应用DCS、PLC、SCADA和MES系统,化工厂能够实现生产过程的实时监控和调节,优化生产工艺,提高生产效率和产品质量。如通过DCS系统实时监控反应釜的温度和压力,PLC系统控制加热和冷却系统,SCADA系统实时监控生产过程中的异常情况,MES系统分析生产数据,提出优化措施。
- 安全管理:通过综合应用DCS、PLC、SCADA和MES系统,化工厂能够实现生产过程的安全管理。如通过DCS系统实时监控生产过程中的各种参数,PLC系统控制安全设备,SCADA系统实时监控生产过程中的异常情况并发出报警信号,MES系统分析生产数据,提出安全管理措施。
六、未来发展趋势
随着工业自动化技术的不断发展,化工厂的控制系统也在不断升级和优化。以下是一些未来发展趋势:
- 智能化:随着人工智能技术的发展,化工厂的控制系统将越来越智能化。通过应用人工智能技术,化工厂能够实现生产过程的智能监控和优化,提高生产效率和产品质量。
- 数字化:随着数字化技术的发展,化工厂的控制系统将越来越数字化。通过应用数字化技术,化工厂能够实现生产过程的数据采集和分析,提高生产过程的透明度和可控性。
- 集成化:随着集成化技术的发展,化工厂的控制系统将越来越集成化。通过应用集成化技术,化工厂能够实现各个控制系统的集成和协同,提高生产过程的自动化和优化管理。
- 网络化:随着网络技术的发展,化工厂的控制系统将越来越网络化。通过应用网络技术,化工厂能够实现生产过程的远程监控和控制,提高生产过程的灵活性和响应速度。
总之,化工厂的控制系统在未来将朝着智能化、数字化、集成化和网络化的方向发展,不断提升生产效率和产品质量,降低生产成本和安全风险。
相关问答FAQs:
1. 什么是化工厂控制系统开发?
化工厂控制系统开发是指为化工厂设计和开发一套完整的自动化控制系统,用于监测和控制化工过程中的各种参数和操作。这个系统可以帮助化工厂提高生产效率、降低成本,并确保操作的安全性和稳定性。
2. 化工厂控制系统开发需要哪些技术?
化工厂控制系统开发需要综合运用多种技术。其中包括传感器技术,用于实时监测化工过程中的温度、压力、流量等参数;控制算法技术,用于根据监测到的数据进行自动调节和控制;网络通信技术,用于实现控制系统的远程监控和管理;以及人机界面技术,用于操作员与控制系统之间的交互。
3. 化工厂控制系统开发有哪些优势?
化工厂控制系统开发可以带来多种优势。首先,它可以实现化工过程的自动化控制,减少人工干预,提高生产效率和稳定性。其次,它可以减少操作员的工作负担,降低人为失误的风险。此外,它还可以实现远程监控和管理,方便管理人员进行实时的数据分析和决策。最后,它可以提高化工过程的安全性,减少事故的发生概率。
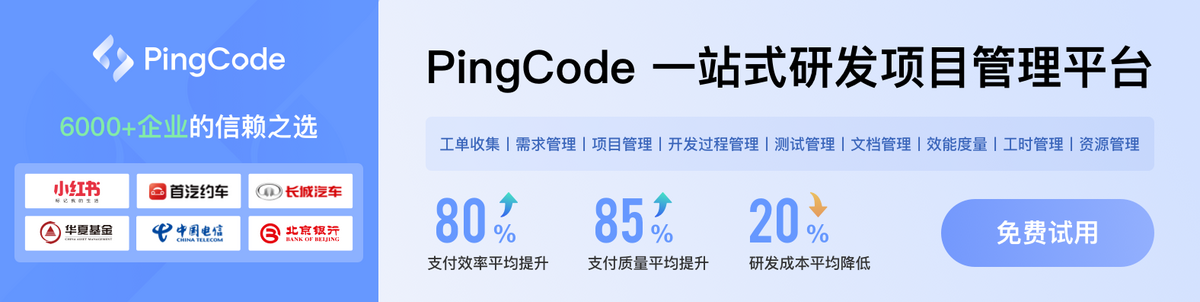